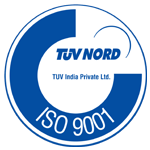
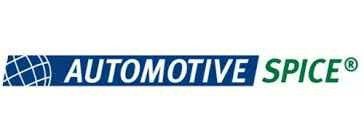
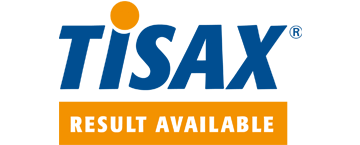
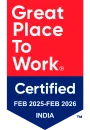
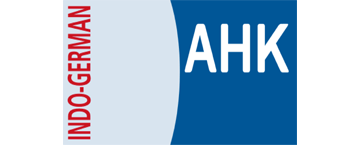
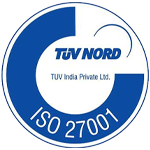
Our Business Engagement Model: Key Benefits
Our pre-tested and ready-to-deploy WWH-OBD software stack (ISO 27145), consists of the following modules:
- ISOTP layer (ISO 15765) and
- An integrated DoIP software stack.
The stack has an edge over an OBD-II solution, as WWH-OBD can be deployed for both passenger and commercial vehicle programs. The baud-rate incompatibility issues in different geographies is also taken care of, as it is a harmonized protocol that caters to different CAN bus baud-rates (125 kbps/250 Kbps).
We offer our WWH-OBD stack solution under a one-time licensing fee model. This engagement model has a slew of benefits that have proved to be value-adds for our customers across Europe, US, India and China.
The following are some of the benefits of one-time licensing model:
- As a customer, you will jointly own the IP rights of the WWH-OBD protocol software.
- This will enable you to deploy the WWH-OBD stack solution in multiple production programs
- This can translate into a substantial cost, time and effort savings in new Product Development and/or R&D initiatives
WWH-OBD Details of the Software Architecture
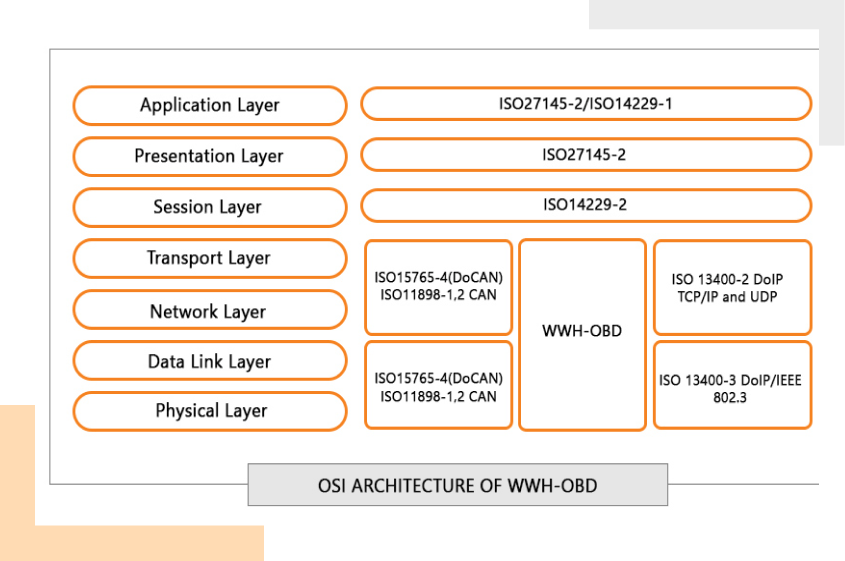
- WWH-OBD (ISO 27145) Architecture highlights the consolidation of DoCAN, ISO TP, DoIP and UDS protocols.
- The Architecture enables implementation across commercial/passenger vehicle and server and client side tooling solutions
WWH-OBD Stack Integration, Configuration and Testing Services
Worldwide Harmonic (WWH) OBD software stack has been designed for both Client (Automotive Tester Tools) and Server Sides (on-board vehicle). Our WWH-OBD protocol stack is a consolidation of entire OBD specifications, which can be integrated with both passengers as well as commercial vehicle applications.
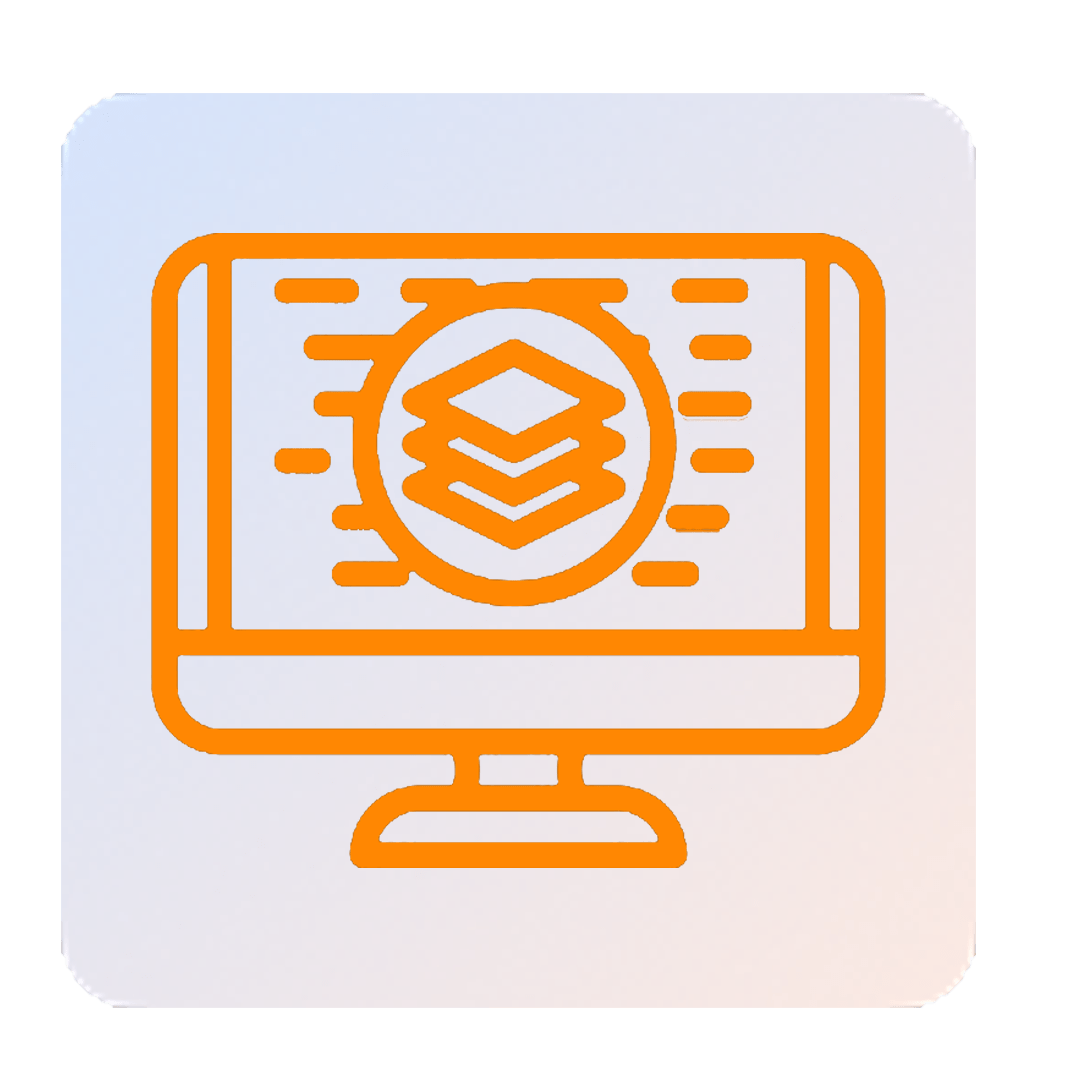
WWH-OBD (ISO27145) Stack Development for Automotive ECUs:
- Implementation of physical layers (CAN and Ethernet)
- Support for OBD modes and PIDs configuration
- Support for Integration of WWH-OBD ISOTP
- Support for both Server and Client-side application development
- Integration with a Ready-to-deploy DoIP Stack
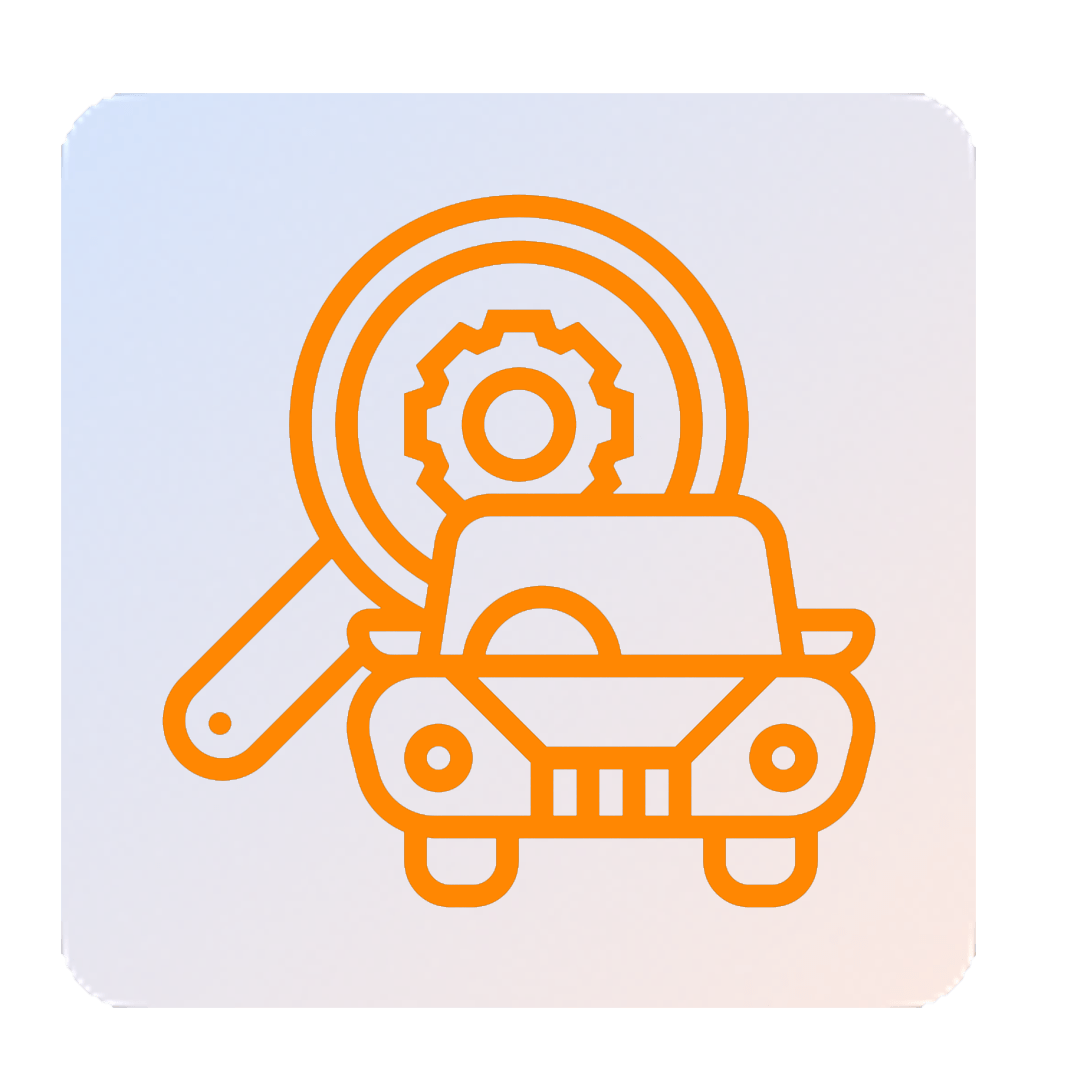
Solutions for Vehicle Data Collection:
- Workshops to develop strategies for vehicle data collection, as per the project requirements
- Functional and design audits for legacy system, if applicable
- Support for data collection for Electric Vehicle (EV) applications
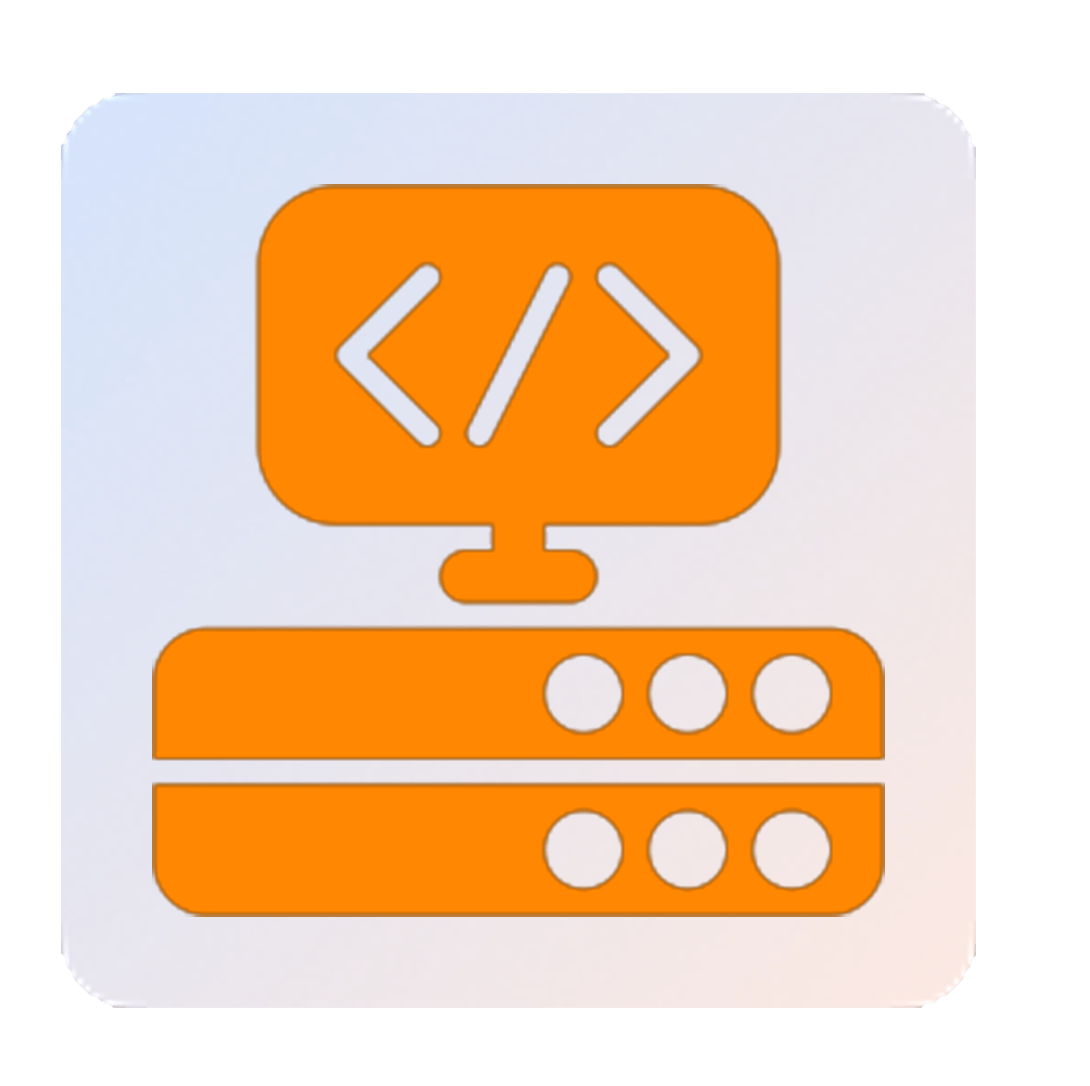
Support for Client-side Tool Development:
- Support for PC Based Tooling System Development
- Support for Mobile Based Tooling Application Development
- Support for Integration of WWH-OBD stack with other client-side tools
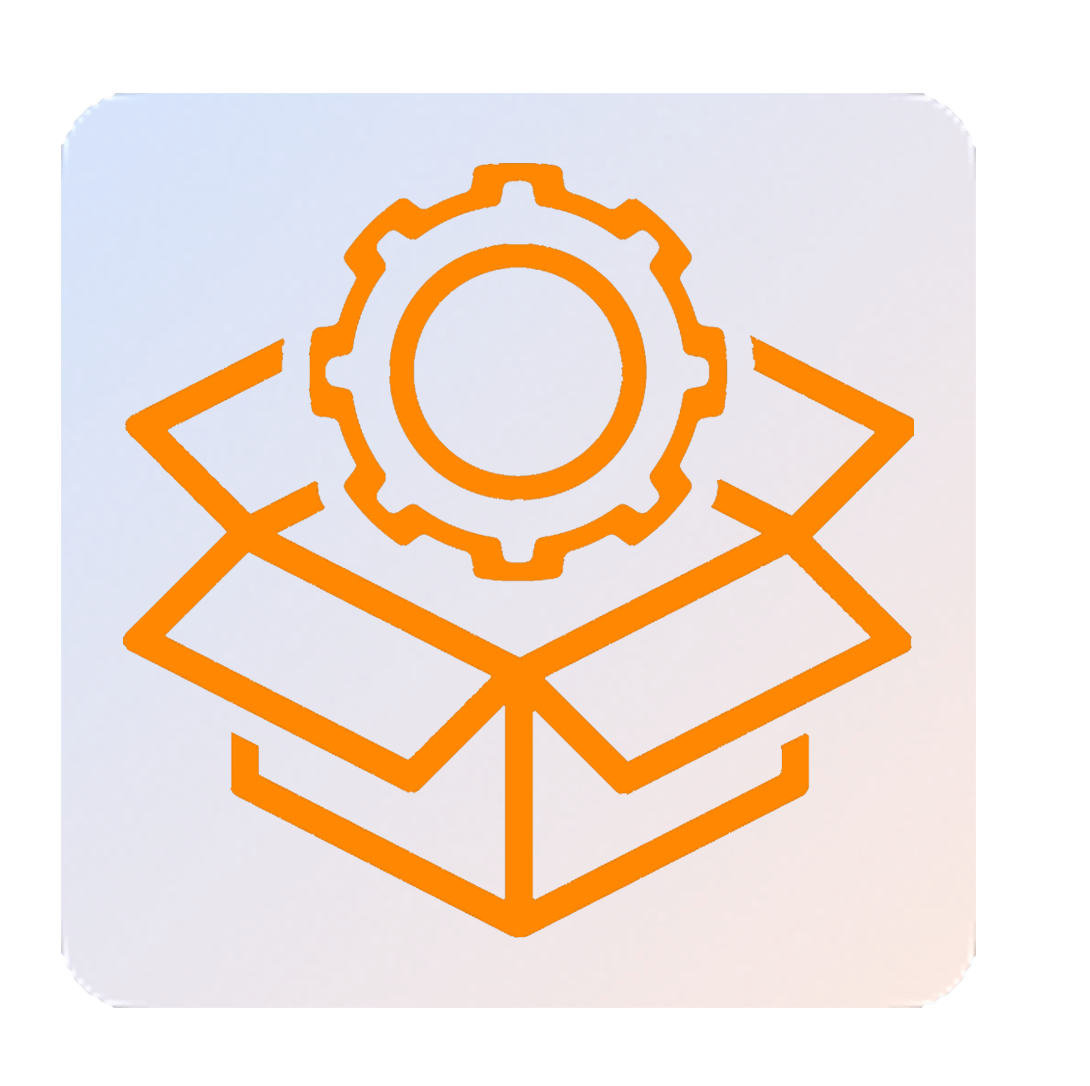
Solution Design for after-market automotive products:
- WWH-OBD stack development, integration and testing services for after-market products
- Integration support for vehicle data collection and processing
- Support for access to vehicle parameters (PIDs)
- Integration, testing and maintenance support for vehicle ECUs like Telematics Control Unit (TCU), ADAS, and BMS etc.
- Support for integration of WWH-OBD stack with Electric Vehicle ECUs.
200+
customers supported since 2010
100+
scalable and reusable Bootloader platforms delivered
30%
quicker time-to-market enabled
95%
lesser development time with PC-based automation tools
Meet Our Automotive Leaders
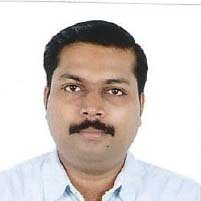
Suresh Kumar
Technical Manager (A people’s Manager)
Suresh is the man with solutions. A pro in multitasking, Suresh is always there for his team and also handles the customers’ problems with alacrity.
Under Suresh, the automotive team has delivered some very critical projects with the biggest OEMs and suppliers. His ability to understand the customers’ pain points and come up with solutions is his biggest virtue.
FAQs Regarding WWH-OBD Software Stack
Ans. Our WWH-OBD software stack has been designed in two variants-
- WWH-OBD Software Stack compliant with CAN Bus
- WWH-OBD Software solution compliant Ethernet Bus
The following software layers will be common to both variants:
- ISO 27145-2 and ISO 14229-1 compliant WWH-OBD services
- ISO 14229 compliant UDS services
WWH-OBD over CAN consists of the following additional layers:
- ISO 15765-4 Diagnostics Over CAN
- ISO 11898-1,2 CAN Drivers and IF Layers
WWH-OBD software stack over Ethernet is integrated with the following additional modules:
- ISO 13400-2 ISO TP and UDP
- ISO 13400-3 DoIP IEEE 802.3 (Wired Vehicle Interface)
Ans. Yes, we provide support for the development and integration of TCP/IP, UDP and MAC device drivers. This facilitates Diagnostics over Internet Protocol. We have ready-to-deploy TCP/IP and UDP stacks, which are Microcontroller Platform independent and can be readily integrated.
Ans . We will provide support in development of CAN IF Layer and CAN drivers. These modules are required for the implementation of WWH-OBD over CAN.
CAN IF configuration is implemented using DBC to auto code generation tool, to reduce development time and cost.
CAN Driver implementation w.r.t microcontroller hardware, is performed as per the project’s requirements.
Ans. Yes, we understand that certain PIDs and DTCs may not be required in your project and you may need project specific fault codes and parameters identifiers.
We have experience in providing support to our customers for customizations w.r.t PID and DTC configurations, as per the requirements of the project.
Ans. Yes. Definitely. We have partnered with customers with such requests in the past.
By the virtue of hardware platform agnostic design and layered architecture, our WWH-OBD stack can be readily ported to your automotive ECU software.
The stack can be easily ported to any microprocessor or microcontroller platform of 16/32 bit. The interfacing between the software modules is performed with the help of API connectivity.
Hence, the stack can be directly linked with the application layer or the base layers of the software.
Ans. Yes, our WWH-OBD stack’s software code is compliant with MISRA C standards . We deploy tools like PolySpace and QAC to ensure this compliance.
Ans. No, the WWH-OBD stack is a completely hardware agnostic solution. Only certain MAC drivers and CAN drivers are required to be designed and developed as per the specific hardware platform.
Ans. Yes, we provide the necessary post-production support and maintenance services.
The Service Level Agreement, warranty period and number of months of support is included in the contract, based on our mutual understanding and project requirements.
Ans. Yes, we provide support for both the client side (Diagnostics Testing tools) and the server-side (ECU applications) application development.
Ans . Both bench-level testing and post-integration (vehicle) testing is provided, as per the customers’ requirements. In the scenario, where we are providing only the stacks and the not the integration services, following reports will be made available:
- Stack-level validation report
- Unit Testing Report
- MISRA-C compliance report
Ans
- Low-level Design Document,
- High-level Design Document and
- Test Reports
These documents are part of the deliverables, along with the WWH-OBD stack. These documents will be very helpful for your in-house teams, during development of new features in future and re-using the stack for integration in different production programs.
Knowledge bytes
What is WWH-OBD?
WWH-OBD (ISO 27145) stands for World-Wide Harmonized On-board Diagnostics.
As the name suggests, this on-board diagnostics protocol is a consolidated standard/specification that includes the specifications for OBD solution which is compatible with both passenger and commercial vehicle.
Another add-on is its capability to handle varying baud-rates of CAN Bus used in different geographies.
Also, the WWH-OBD protocol is supported over two physical mediums- CAN and Ethernet (DoIP). This protocol is the latest new step taken by the industry, towards standardization across the automotive sector.
It also makes life easier for the client-side tool manufacturers, as they now have to build testing tools that need to support only CAN and Ethernet.