About the Customer:
Our customer is an Indian Automotive Tier-1 Supplier, a pioneer in brake system development and manufacturing. Taking a lead in safety critical automotive components development, they are developing an ASIL-D compliant brake system ECU.
Business Challenges:
The vision to replace manual parking brake with electronic parking brake was not merely about enhancing the vehicle's aesthetic and comfort. It was also about leveraging technology to improve safety, reliability, and user experience in line with modern automotive standards.
Key Challenges in Developing the EPB System:
Complex Algorithm Development using MATLAB:
- Development and validation of a comprehensive suite of algorithms for seamless EPB operation.
- Required intricate logic and extensive testing for a range of functions from basic braking to advanced safety.
- MATLAB expertise was required.
ISO 26262 ASIL D Compliance:
- Achieving the highest safety integrity level (ASIL D) under ISO 26262 standards.
- Necessitated stringent development processes, rigorous testing, and detailed documentation.
- A number of safety analyses to be performed including FMEA, FMEDA, FTA and DFA in a stringent time frame.
Integration with Existing Vehicle Architecture:
- Seamless integration of the EPB system into diverse vehicle architectures without compromising performance.
- Demanded adaptable design strategies and extensive OEM collaboration to meet varied integration requirements.
Embitel’s Solution:
Since we were providing end-to-end development of the electronic brake ECU, we followed the V-lifecycle starting with deriving the software safety requirements and functional requirements.
In the next step, our FuSa team identified the safety activities required for the execution of an ASIL D project. The activities included devising a safety plan, preparing the Development Interface Agreement (DIA) and Data Management Plan (DMP). Since it was an end-to-end project, a cross-functional team comprising hardware and software engineers along with ISO 26262 experts was set up.
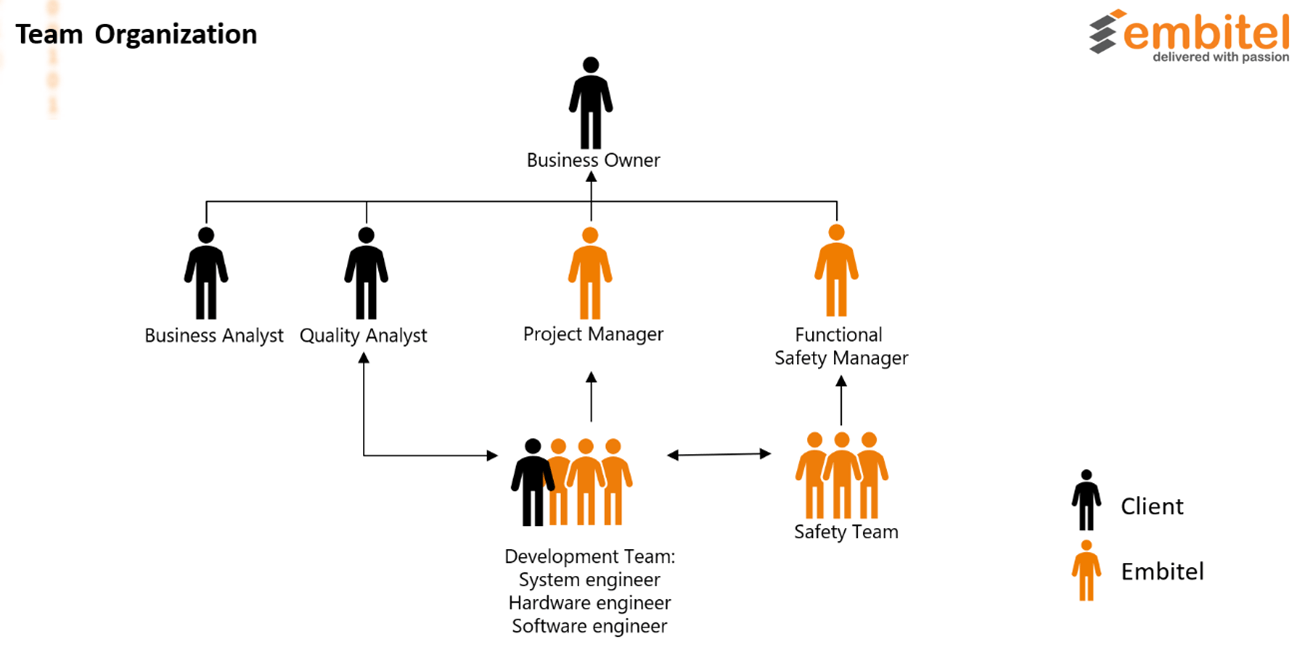
After a few joint workshops with the customer’s team, we were clear with the requirements. Documentation of the system-level requirements were performed while we kick-started the concept and system phase of the safety lifecycle. Here is a snapshot of the steps included:
- Item definition: Based on the information provided by the customer we derived the item definition of the brake system. It paved the way for HARA and helped in the development of functional and technical safety requirements.
- Hazard Assessment and Risk Analysis (HARA): We assessed the malfunctions that could possibly lead to E/E system hazards and analyzed the risk associated with them.
- Safety Goals derivation: Safety goals were derived as the output of HARA analysis.
- Development of Functional Safety Requirements (FSR) and Technical Safety Requirements (TSR): We derived the FSR from the safety goals and TSR from functional safety requirements.
Based on the safety goals, TSR and FSR, system architecture was prepared which followed the software and hardware architecture along with BOM creation.
Software Algorithms Developed for ASIL D Compliant EPB Solution:
A manual parking brake, when replaced by its electronic counterpart, creates a gamut of scenarios to be addressed.
We built certain algorithms to manage these scenarios, especially those which are related to functional safety.
- Auto-Apply: If ignition is off, EPB is auto-applied
- Manual Apply/Release: Manual apply and release only when vehicle speed < 5kmph, service brake pressed etc.
- Auto-Apply on drive away: If vehicle speed > 5kmph, driver’s seatbelt is fastened and multiple other conditions met, EPB will be released automatically.
- Controlled Deceleration: EPB applied when vehicle speed > 5kmph, a controlled deceleration will be done instead of instant brake application.
- Gradient based EPB apply: The intensity of brake force will depend on how inclined the slope is. This reduces brake wear and tear.
- Auto-hold feature: This feature enables automatic press and release of EPB. The EPB is pressed when the vehicle stops and released when the vehicle resumes driving. Thise feature is a great comfort feature when driving in traffic or on a slope.
We implemented scores of such algorithms to ensure comfort of the driver and functional safety of the system.
Overview of the solutions and services provided:Electronic parking brake software development
- Software & system FMEA and DFA
- Base software development including HAL & COM layer, device drivers, low level drivers & safety and diagnostics layer
- ASIL D compliant Firmware development to control motors for electronic brake ECU
- MATLAB powered development of software modules for application layer.
- Unit, integration and functional testing with reports
Electronic parking brake hardware development
- Hardware FMEDA and FIT calculation
- Hardware schematic design
- Board bring-up
- PCB layout and Gerber file generation
- Compliance, simulation, and functional testing
A Snapshot of Technical Approach for Electronic Brake ECU Development
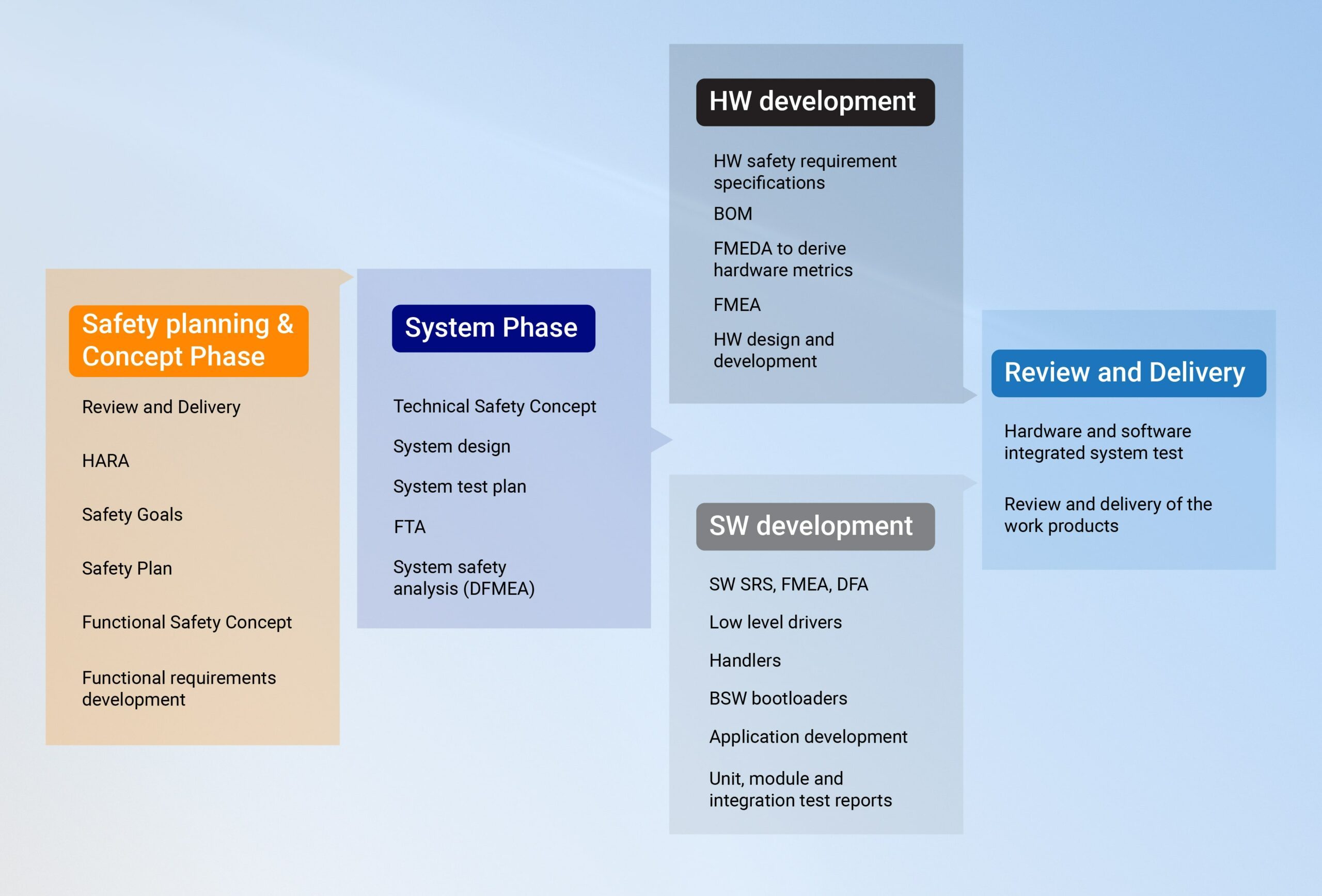
Embitel Impact:
We provided the customer with complete software and hardware development support as per ASIL D requirements. Being a one-stop destination for both software and hardware development and ISO 26262 compliance activities, we were able to provide an end-to-end solution to our customer.
The following ready-to-integrate components aided in reduced turn-around time:
- UDS protocol software stack with configuration and integration support
- Readily available board support package for Infineon Aurix family of microcontrollers
Tools and Techniques:
Codebramer ALM Tool: We used Codebeamer for application lifecycle management
MATLAB from Mathworks: MATLAB was used for software modelling
ENCO SOX: Used for safety analyses like FMEDA, DFA etc.
Tessy tool: An ISO 26262 qualified tool for unit and component testing
Polyspace: Static code analysis tool
Cadence: Tool for PCB layout