ISO 11898 CAN BUS
Protocol Software
A Ready-To-Integrate CAN BUS Protocol
Software To Power ECU Communication
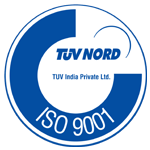
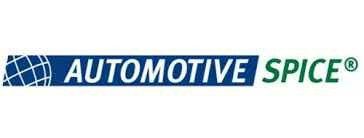
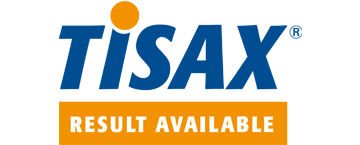
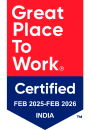
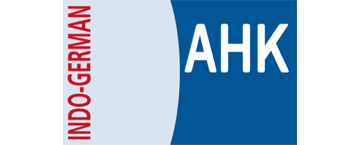
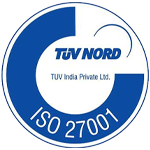
Enabling Faster and Reliable In-Vehicle ECU Communication
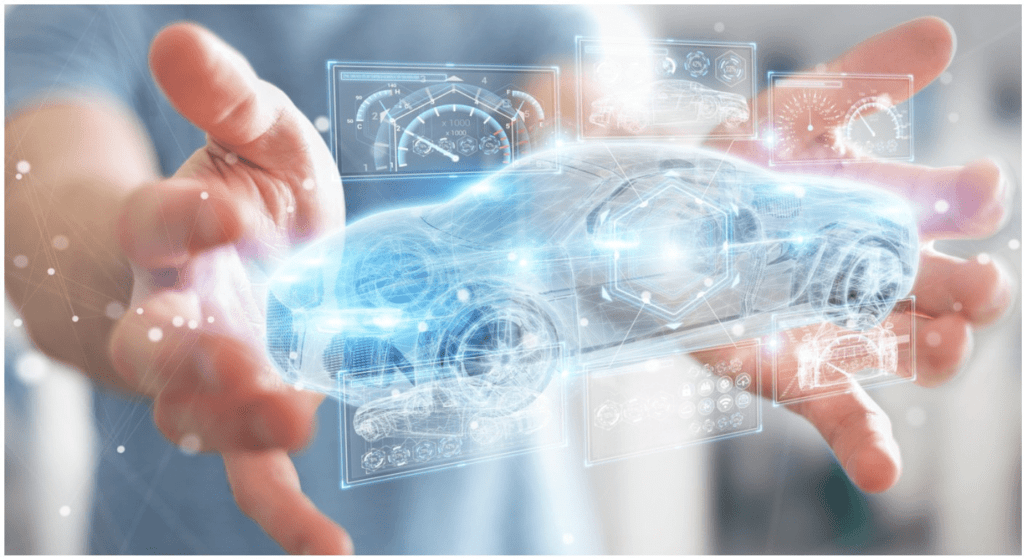
Embitel’s CAN Protocol Stack
Embitel offers a ready-to-deploy CAN BUS protocol software package based on ISO 11898 standard. With our production-grade CAN BUS stack, you can implement ECU communication capabilities in your automotive solutions development program with reduced turn-around time.
This CAN Bus protocol stack is ideal for supporting in-vehicle networking functions, within passenger vehicles.
We offer this CAN Bus Protocol stack under a one-time licensing fee model. This engagement model has proved to be a great value-add for our customers across US, India, China, Taiwan, South Korea, and Europe.
Know more about our CAN BUS protocol software business model, features,
use-cases, and technical specifications.
Striking Features of our CAN BUS Protocol Stack
- Our CAN BUS protocol stack has a modular architecture making it simpler to integrate to your existing automotive system and hardware.
- The CAN BUS stack is implemented in ANSI-C and is independent of the CAN controller, CPU and operating system.
- Unit, Integration and Functional testing of SAE CAN BUS with relevant tools are performed and test reports are shared with the customer.
- CAN BUS interface layer and Network Management layer are pre-tested and pre-packaged as per the ISO 11898 standard. These layers are ‘re-usable’ for any automotive ECU and/or automotive tooling applications.
- CAN BUS protocol software code is compliant to 2012 MISRA C standards.
- We offer our industry recognized SAE CAN BUS protocol software under a one-time licensing fee model.
- Terms & conditions regarding IP rights and source code ownership are completely transparent and fully aligned with the customer’s requirements and vision.
- Our CAN BUS stack finds application in implementation of ECU communication for all kinds of vehicle ECU and automotive systems.
- We have delivered our CAN bus protocol software for Seating ECU, Body Control Module, Telematics, Powertrain and so on.
Embitel’s Service Offerings for SAE CAN BUS Software and its Integration
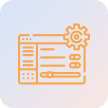
Development and Configuration of CAN Bus Interface Layer (CAN IF)
- Ready-to-deploy CAN Bus Interface layer (CAN IF); only configuration is needed
- DTx and Rx message configuration from the CAN DBC file (CAN Matrix)
- Support for Tool based/ manual configuration of CAN Interface layer (CAN IF)
- Configurable Skeleton code (.C, .F, cgf.c and cgf.h) of CAN Bus Interface layer (CAN IF) is also available
- Low level and high level documents are provided
- Support for software level message filtering
- Signal and message extraction provided as a default feature
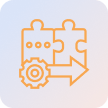
Development and Integration of CAN Bus Device Drivers
- Support for all Microcontroller Families (Renesas, TI, Fujitsu etc.)
- Supports 29- and 11- bit identifiers
- Hardware Filtering (Acceptance Filtering) of messages and signals
- Support for standard baud rates of 125kbps, 250 kbps and 500 kbps
- Leverage Reusable components of CAN BUS device drivers to reduce time-to-market
- Support for CAN BUS device driver integration, across production programs
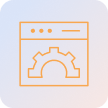
Integration and Configuration of CAN TP (ISO 15765) and Network Management Layer
- Message and mode monitoring
- Checksum strategies to ensure message validation
- Integration of UDS (ISO 14229) stack over CAN TP (ISO 15765)
- Customizations as per your business requirements
- Built-in error handling feature of CAN BUS
- Ready-to-deploy CAN TP layer for reduced turnaround time

CAN Bus Protocol Stack Testing Support
- Creation of High Level Design documents (HLDD) and Low-Level Documents (LLD)
- CAN Conformance Testing of Data Link Layer with Vector tools like CAN Stress
- Design of Integration and Functional Test Plans
- Support for MISRA compliance report creation
- End-to-end Testing Services (Unit, Integration and Functional Testing)
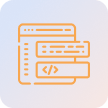
Design and Development of PC Based Auto Code Generator Tool
- CAN DBC File to configuration file generation tool
- Auto Generated and MISRA C compliant code
- Code generated in fraction of seconds
- PC based (Windows) tool
- Easy to remove Tx and Rx messages from the CAN Matrix
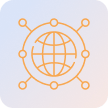
Multi-channel CAN Configuration tool
- We have developed a CAN Interface layer configuration tool with capability of simultaneous configuration of 4 CAN channels using different DBC files
- Supports use cases where dynamic configuration of the CAN interface layer using the CAN DBC files is required
- Configuration files for all 4 CAN channels can be simultaneously generated
- Network nodes inside the DBC files can be selected before the configuration
- Schedule time, message queue size can be customized for each configuration
200+
customers supported since 2010
100+
scalable and reusable Bootloader platforms delivered
30%
quicker time-to-market enabled
95%
lesser development time with PC-based automation tools
Embitel’s Advantage
Industry-wide Recognized
We have integrated CAN BUS stack for several production programs across the globe. The extensive experience gives us an edge in the implementation of ECU communication through CAN BUS.
CMMi Level 3
Certified
As a CMMI level 3 certified organization, we have a robust process model in place. This ensures that the CAN BUS stack along with other stacks are reliable, bug-free and efficient.
Configuration & Integration Support
Our CAN BUS protocol software is designed to be fully configurable as per project specifications. We provide support for configuration of Tx and Rx messages through CAN IL tool.
Support &
Maintenance
Our CAN BUS stack integration service comes with a well-defined support and maintenance process. The post- integration support begins as soon as we integrate the CAN BUS stack with your projects.
Related Blogs: Learn More About CAN Bus Protocol Stack and In-vehicle Networking
- What is CAN BUS Protocol Stack? And Why it is a Critical Software Solution for Electronic Control Unit (ECU) Communication?
- [Vlog] Learn All About CAN BUS Protocol Stack: An Invisible Hero, Omnipresent in Your Automobile!
- [Vlog] Want to Understand CAN Interface and CAN NM Layers? The Layered Architecture of CAN BUS Protocol Stack has All the Answers
FAQs About CAN Stack Solution
- Low-level drivers (CAN, MCU, EEP, Timer)
- CAN Bus Software Stack (CAN NM and CAN Bus Interface)
- ISO TP Layer (ISO15765)
- UDS Stack (ISO 14229)
- Application Layer
- Bootloader Application Layer
- UDS Based Bootloader Software
- CAN Device Drivers support 11&29 bit identifiers
- In-built Interrupt Based data handling
- Data Queuing feature
- APIs for Tx and Rx messages
- CAN Bus Interface Layer (CAN IF) w.r.t CAN Matrix
- Supports Signal Extraction
- Supports S/W filtering CAN Network Management
- Message and node monitoring
- Sleep/Wake up functionalities
Ans. CAN BUS Device Driver is the only part of the stack that is dependent on the hardware platform. Rest of the software layers, like CAN IF and CAN NM are hardware agnostic.
It implies that the CAN driver will need to be developed based on the microcontroller used in the project.
Our automotive team has expertise of developing device drivers for all major MCU families including Renesas, Fujitsu, TI and others.
- Seating control ECU,
- Engine Control Unit and
- HVAC systems
Ans. Yes. Our service level agreement for CAN Protocol Stack clearly documents the fact that we will provide all the necessary configuration and integration services, along with CAN protocol stack license.
Tool-level integration for low-level drivers as well as application level, will also be a part of our SLA.
- Unit level Testing
- Functional Testing
- Data Link Layer Compliance testing using vector tools
Ans. Depending on the size of the CAN Matrix file, we use manual method or an automation framework/ tool for conversion from CAN DBC file to configuration file code.
Our proprietary PC based auto-code generator tool, is capable of generating configuration files instantly as compared to manual method that would take 2-3 weeks.
As a customer, you have the freedom to choose between the manual method and the tool-based method.
- The auto-generated code is MISRA C compliant.
- It takes a few seconds to auto-generate the code.
- Development time and cost is reduced considerably.
Ans. Our CAN BUS Software stack is designed to be a light-weight software. The size of flash memory is 6 kB and RAM size is 1 kB.
However, the RAM size will depend on the stack configuration. This configuration will be unique, as per your business application needs.
Bigger the CAN configuration file, higher is the RAM memory.
Ans. Yes, by the virtue of its design, the CAN BUS software solution is modular in nature. Our coding guidelines ensure that no global variables are exchanged between different source files.
Each functionality is invoked using an API. The modular nature also makes our stack lightweight in size.
- The Library Format of the stack will not comprise of any editable source code.
- You will not be able to re-use the same CAN software stack solution for any other production programs.
- The Library Format of the stack will not comprise of any editable source code.
- You will not be able to re-use the same CAN software stack solution for any other production programs.
Knowledge bytes
- What is a CAN BUS Protocol Stack?
- CAN Stack is an in-vehicle networking (BUS) standard, which allows the various electronic control units to communicate with each other. CAN Stack is a serial communication protocol for passenger vehicles.
- It allows considerably higher data rates in tune of 500 kbps. Using the CAN Transport layer (ISO 15765), the data rate can be further increased.