Motor Control Software & Hardware
Development - BLDC, PMSM, AC Induction Motors
During our journey of more than a decade in the Automotive Industry, we have developed a robust ecosystem for delivering quality Motor Control Software solutions.
These include Brushless DC Motor Controller and PMSM Motor Control Solutions
This ecosystem consists of experienced Embedded Software and Hardware Engineers, Automotive Domain Experts and Industry Partners.
For more than 12 years, our focus area has always been Product Engineering Services (Embedded Software and Hardware design services). This has facilitated our team to develop in-depth expertise in Model Based Development and in delivering Functional Safety (ISO 26262) and AUTOSAR complaint solutions.
We have partnered with customers to develop electronic based motor control development for Electronic Power Steering (EPS), Seating Control, Smart Actuator for Turbo Chargers and other applications.
Expertise in types of Motors
- Permanent Magnet Synchronous Motor (PMSM)
- Induction motor
- Single Phase and 3 Phase Motor
- DC motors (Brushed) in power window.
- Brushless DC Motors (BLDC) deployed in Electronic Power Steering, Seating Control etc.
- Expertise in DC motor controller – Torque Speed characteristics/PID tuning
A Handbook on Motor Control System
Learn about Reference Design Solution of our
Motor Controller, its salient features and use cases
A Handbook on Motor Control System
Learn about Reference Design Solution of our <br>Motor Controller, its salient features and use cases
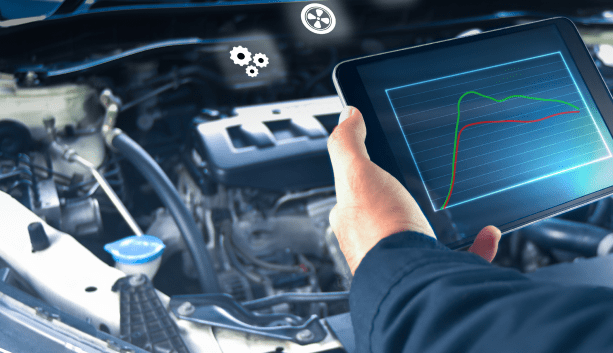
Our Motor control software and hardware development expertise
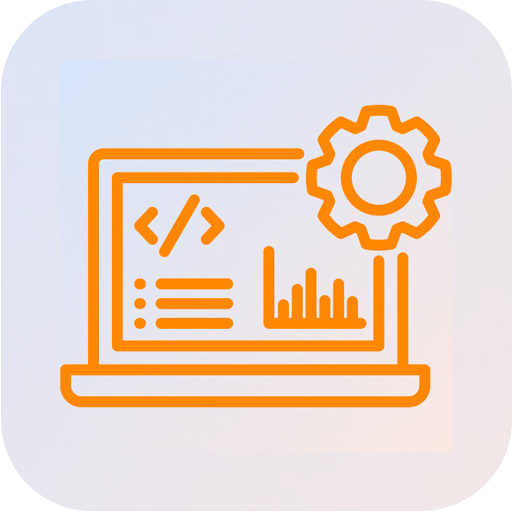
MCAL / low-level Driver Development
- Low level drivers such as ADC,MCU,SPI,I2C,PWM,ICU,and NVM
- CAN and LIN Drivers
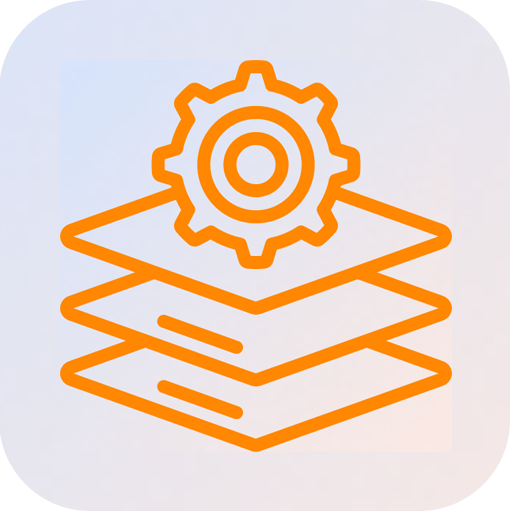
BSW Layer Development
● Off Board Diagnostics (UDS,J1939 etc.)
● Fault Code Memory
● Safety Mechanisms
● Hardware Abstraction Layer
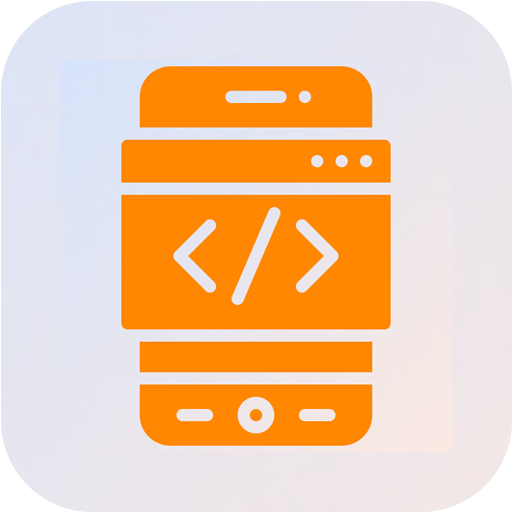
Application Software Development
● AUTOSAR based application software development
● MATLAB based application software development
● Non-AUTOSAR based application software development
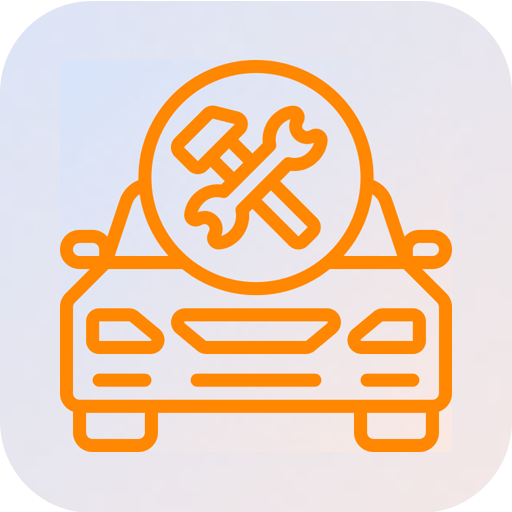
AUTOSAR and Vehicle Diagnostics Support
● Ready-to-deploy & re-usable software stacks and Bootloader solutions for in-vehicle communication and diagnostics (CAN, LIN, UDS, KWP2000, Serial, BT)
● AUTOSAR and non-AUTOSAR compliant Base Software Development
● AUTOSAR compliant application software
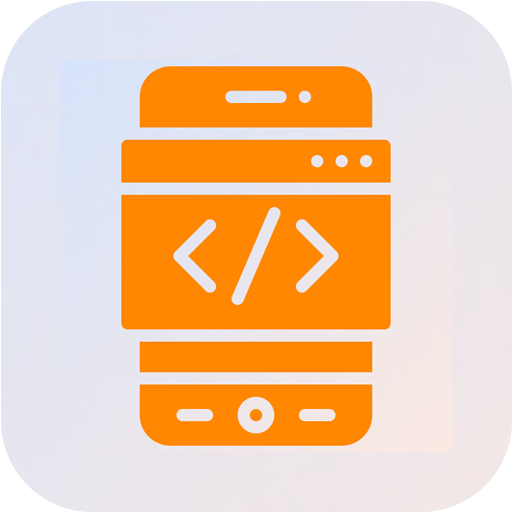
Functional Safety
- Safety Lifecycle in parallel with SDLC
- Support for ASIL D certification
- Safety Activity planning and execution
- ASIL compliant documentation, verification and validation
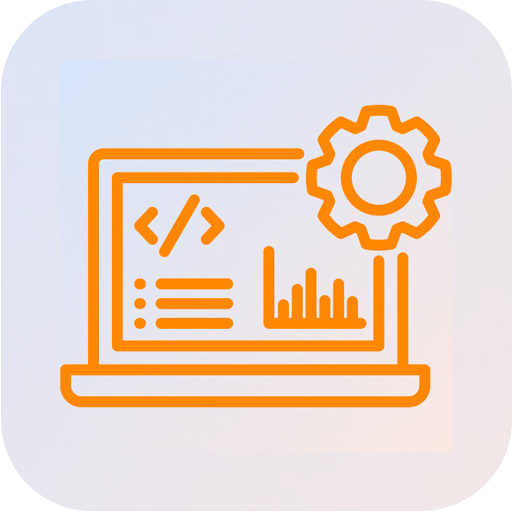
Application Software & Motor Control Algorithm Development
- Speed Regulation
- Pulse Width Modulator
- Current Regulation
- Field-oriented Control (FOC)
- Proportional Integral Derivative Controller
- Direction control
- Soft Start/Stop
- Software Start/Stop
AUTOSAR and Non-AUTOSAR compliant Base Software (BSW) development support
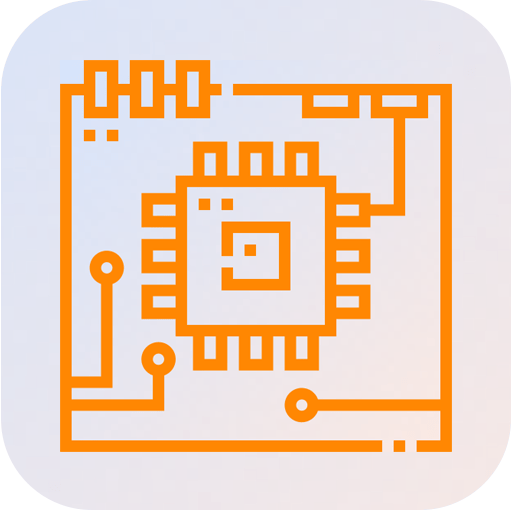
Hardware Design & Consulting Services
- Microcontroller
- Torque & Angle Sensors
- HALL Effect sensors
- Gate Driver IC
- Temperature Sensors
- Pre-driver Components
- H-Bridge (MOSFETs)
Automotive Grade Hardware Development, Support for EM and Thermal Analysis
Motor Control Development Success Stories
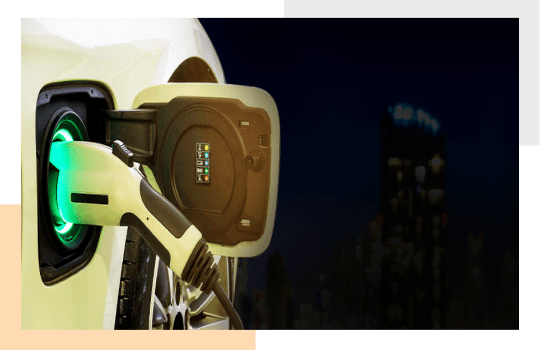
An End-to-End Actuator Design Solution for a Throttle Control Unit (ECU)
Embitel collaborated with a leading U.S. Automotive Supplier to develop a robust Throttle Control ECU Actuator. Overcoming challenges through Value Engineering, we delivered a cost-effective, reliable solution, reducing time-to-market and overall project costs.
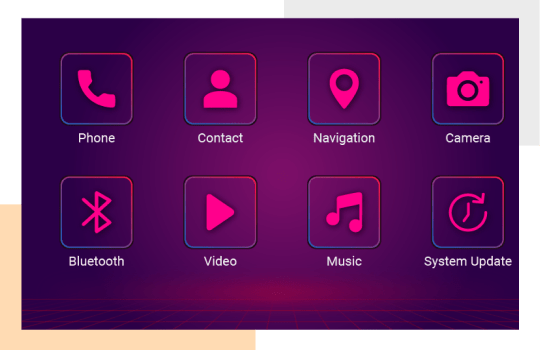
Motor Control Software and Hardware Development for an Electronic Power Steering (EPS) System
We successfully developed a Proof-of-Concept (POC) for a Europe-based Tier-1 Automotive Steering Solutions Supplier, achieving a rapid 3-month completion. We helped the customer overcome challenges in creating ISO 26262 ASIL-D compliant Electronic Power Steering hardware and software, integrating J1939 stack, and addressing issues in the test-bench. This showcases our expertise in motor control software development.An automotive Tier-1 Supplier, wanted to develop a cutting- edge Android Infotainment System for their commercial vehicles with quick time to market.
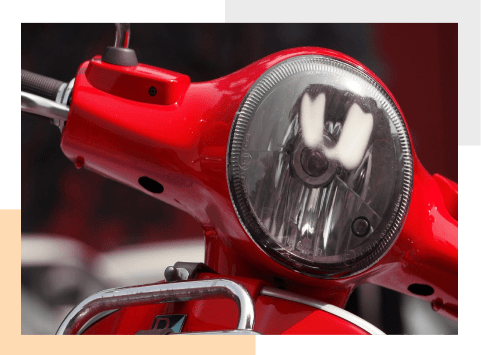
Development of Motor Controller and Application Layer (using MATLAB), for BLDC Motor
This is the story of how we addressed a leading electric motor supplier's challenge in developing a Brushless DC (BLDC) motor controller integrated with a transmission control unit.
Leveraging MATLAB model-based development and SimScape for simulations, Embitel's engineers optimized motor parameters, reduced hardware components, and seamlessly integrated the BLDC motor controller software. They delivered a high-performance motor controller solution with cost and time savings for the customer. .
Video Explaining Motors as the Power and Motion Delivery System in a Vehicle
AUTOSAR, Partial AUTOSAR and non-AUTOSAR Software Architectures
Depending on the project specification, we can help you follow any of three approaches in automotive motor control software architecture:
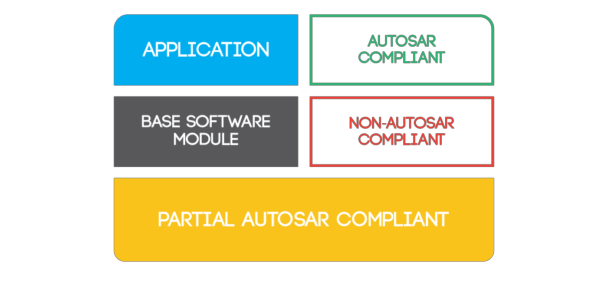
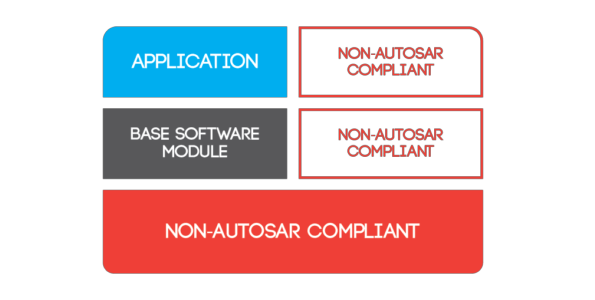
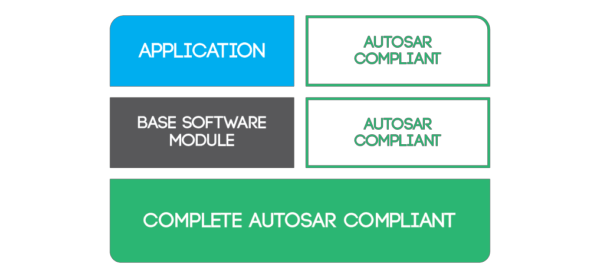
Steps Involved Motor Control Hardware Design Process
Tools and Technologies Expertise
- MATLAB, Simulink, Stateflow, RTW, E-coder
- PIC, Renesas, Fujitsu, Freescale controllers
- Fujitsu, PIC, Renesas tool chains
- Renesas RL78/F-13 Family Microcontroller
- IAR Embedded Workbench
- ORCAD: Schematic Design
- Simscape: Used within Simulink to create model of physical systems
- Allegro: Layout
- Hyperlynx 8.0 : EM and Thermal Analysis
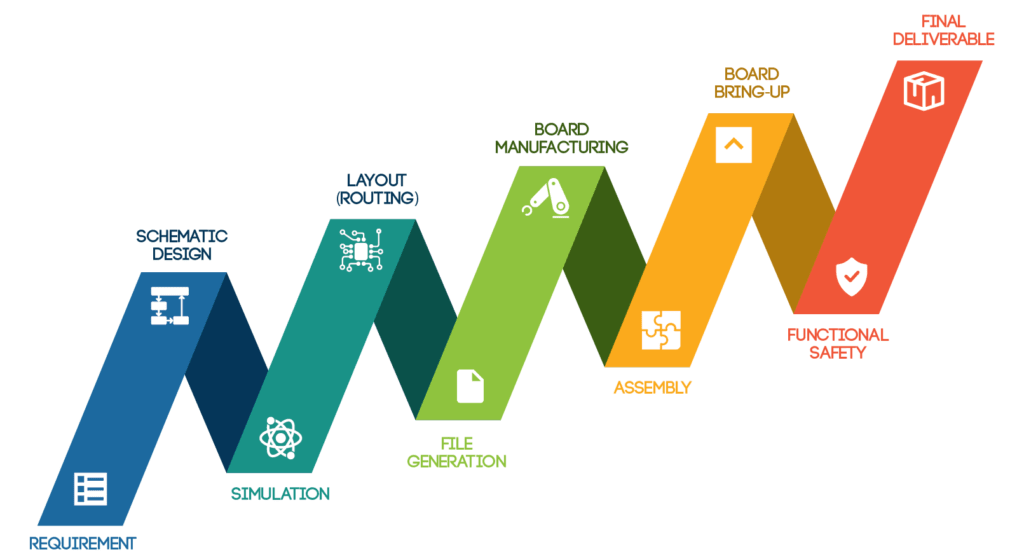
Related Posts: Learn More About our Motor Control Development Services for Automotive Products
- Automotive Motor Control System: The Brain Behind the Brushless DC Motors in an Automotive Application
- Brushless DC Motor vs PMSM: Find Out How These Motors and Their Motor Control Solutions Work
- [Video] All About Motors: The Power & Motion Delivery System for Automotive Applications
- [Video] Meet Motor Control System: The Brain behind the Automotive Motors
- [Webinar] What Is Regenerative Braking and How Is It Achieved in an Electric Vehicle?
FAQs Regarding Motor Control System Development
Ans. Yes, our team has the necessary skill-sets, automotive domain expertise and project experience for delivering an AUTOSAR complaint < href="https://embitel.com/motor-control-solution-for-electric-vehicle-drivetrain" target="_blank" style="color: #FF8702">Motor Control Solution.
We have integrated robust and production grade versions of third party stacks like BSW and RTE software for AUTOSAR projects in the past.
Our team will collaborate with you to develop the Automotive Application as per AUTOSAR compliance. We will also support in development of MCAL and CDD modules
We provide support for every aspect of the Functional Safety Lifecycle and also perform FMEA, HARA, and hardware FMEDA for motor control systems.
We have worked with leading Automotive Suppliers and OEMs’ for ASIL compliance of a motor control ECUs’ in the past.
Ans. Our team has been working on multiple projects, where we are developing software solutions for global production programs of Electric Vehicles
For such engagements, we have been partnering with customers for design of Motor Control Software and Hardware modules for Electric Vehicle programs in Asia, US and Europe.
The choice of MCU to be used rests with the customers, however, we also provide consultation to help you choose the most suitable platform.
Ans. A few of the diagnostics features that we have implemented in our motor control system projects include:
- Short protection like short to GND, Short to VBAT and Open Circuit
- Based on any diagnostic errors, Drive circuit is completely OFF or Limited Drive controlled by Software.
Based upon the specific requirements of the project, we also add more diagnostics features.
Knowledge bytes
- What is an Automotive Motor Control System?
How do you think the new power steering system work with minimal force applied by the driver? How does a seat go forward, backward, up and down with a push of a button? The answer of both these question is the automotive motor control system.
In the simplest terms, a motor control application is a set of hardware and software components that drive a motor or multiple motors. These motors, in turn, perform actions such as opening-closing of windows, power steering movement and more.
Depending on the type of motors to drive, these motor control systems can be a Brushless DC Motor Controller or PMSM Motor Control Solutions.
Types of motor control system
- Open Loop Motor: The motor control applications in which the quality of the output does not impact the input to the motor control process is called an open loop motor control system. It implies that they are open-ended system that do not have any feedback mechanism.
- Closed Loop Motor: A closed loop motor works on feedback mechanism and hence, it is also called feedback control system. An error signal is generated by the Gate Driver IC in case the actual output is different than the desired output. This error signal will go to the motor controller which will take necessary actions. In a way, it is a self-correcting motor control applications.
- What are the components of a Motor Control System?
Gate Driver Unit: This Integrated Circuit acts a power amplifier. It will accept a low-power input from the motor controller IC and gives high-power input to a switch that transfers it to the motor.
MOSFETs: These are switches that will again amplify the signal received from the gate drivers. This signal will be passed to the stator of the motor causing an Electro Magnetic Flux, EMF.
H-Bridge: H-bridge is again a circuit that helps a DC motor to run in both clockwise and anti-clockwise. It can apply the voltage to a load in any direction and this how it controls the direction of the motor.
Motor: Motors can be DC, AC, Brushless, brushed etc. They are used depending on the use cases and the application.
So, in order to run the motor, a set of data (PWM signals) flows from microcontroller to the motor via the gate drivers and MOSFETs.
- What are the different applications of EV Motor Controllers?
The EV motor finds multiple uses in the entire automotive industry –
- Electric Cars – The Mainstay in EVs: In the world of electric cars, motor controllers are like the conductors of an orchestra. They dictate the tempo, ensuring your EV accelerates smoothly, cruises efficiently, and regenerates energy during braking.
- Electric Bicycles (E-bikes) – Boosting Pedal Power: E-bikes are the rebels of the bicycle world, with motor controllers turning ordinary bikes into electrifying rides. They provide that extra oomph when you need it most, making uphill climbs feel like a gentle breeze.
- Electric Scooters – Urban Mobility: Picture zipping through city streets silently and efficiently. That’s the magic of electric scooters, where motor controllers ensure you have a comfortable and responsive ride, perfect for navigating congested urban areas.
- Electric Boats and Personal Watercraft – Sailing into the Future: On the water, motor controllers are the captains of electric boats and personal watercraft. They provide the thrust and control needed for silent and eco-friendly boating, offering serene journeys across lakes and oceans.