Modern day cars are highly influenced by the advancements in digital technologies and unique consumer demands. All innovations in the Automotive domain are currently being driven by the following three principles:
- The industry is increasingly moving towards offering more personalised experiences to drivers and passengers alike.
- Innovative solutions are being developed to ensure seamless connectivity between the vehicle and external devices.
- Processes and features are being implemented to ensure driver assistance and safety are given top priority.
In line with the above principles, there are some recent trends that have redefined the status quo in the industry. The digital cockpit is such a trend that has created waves across the automotive industry!
In this blog, we explore the components that constitute a digital cockpit in cars and the underlying technology stack that powers it.
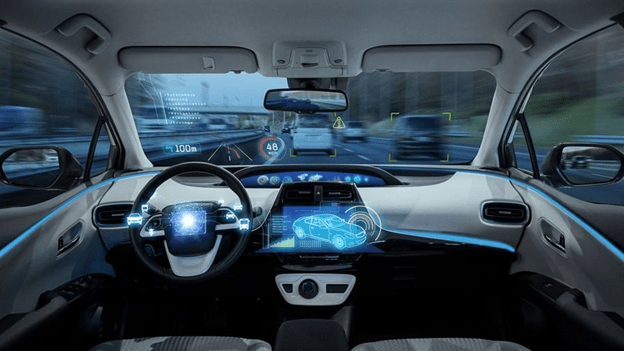
Digital Cockpit – A Revolution, Powered by IoT and Automotive Electronics
What is Digital Cockpit? Let’s understand this first.
A Digital Cockpit solution is designed to offer a Unified Digital Experience, by breaking the silos between the various in-vehicle interfaces.
Hence, a Digital Cockpit is the coming together of interfaces like instrument cluster, Heads-up Display (HUD), HVAC and Infotainment systems.
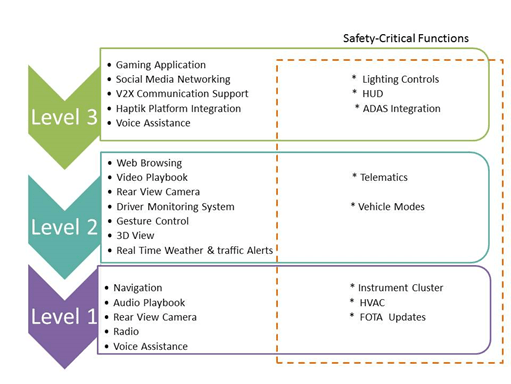
What was the need for a Unified Digital Cockpit Solution?
- ECU (Electronic Control Unit) Consolidation: When in silos, the instrument cluster, infotainment system, and HVAC system are being powered by Multiple Control Units, different operating systems and software modules. With the introduction of Digital Cockpit in cars, the task of Automotive ECU consolidation was effortlessly achieved. With Digital Cockpit, all these interfaces can be powered by using a common micro-controller platform/ System on Chip Platform.
This reduces the complexity related to automotive electronics.
- A Digital Cockpit solution, consisting of Digital Interfaces allows OEMs to overcome the limitations of Analog Instrument Cluster and other interfaces. With Digital HMI, automotive OEMs and Suppliers gain the liberty to design interfaces which deliver more relevant representation of real-time data. Digital Interfaces also extend the scope to support various safety-critical features.
Understanding the Technology Stack that Powers a Digital Cockpit
- The Hardware Module:
The hardware design of a car cockpit may vary between auto manufacturers. However, we can still analyse the basic components of the hardware architecture of a Digital cockpit.
- Application Processors: The modern digital cockpit system has intense processing power to accomplish various functions. For example, managing multiple audio and video input/output, managing the ADAS and driver monitoring features, powering speech and image recognition capabilities, supporting real-time navigation & more.
- This calls for highly powerful and flexible application processors. OEMs usually look for high performance Application processors that are optimized for RTOS and virtualization. They also need to demonstrate efficient Signal, image and vision processing capabilities.
- Another major aspect to look for while choosing Digital Cockpit Processor is how well it can balance the safety critical requirements along with processing requirements. This is essential especially for performing time and safety critical operations like auto braking to avoid a collision.
- Jacinto DRAx automotive processors and Cortex-A76 -Arm processors are some of the leading Digital Cockpit processors in use today. Many OEMs are going the multi-core processor way to fulfil the intense processing and safety requirements of a Digital Cockpit.
- System On Chip: Many modern digital cockpit solutions are based on System on Chip (SOC) that enable three individual boards to manage the infotainment system, the instrument cluster, and the Heads-Up Display. This approach helps them save considerably on cost and development cycles. The typical SoC used for digital cockpit solutions includes multimedia accelerator, memory, Graphical Processing Unit, automotive peripherals, connectivity interfaces and digital signal processor.
TI’s new and powerful Jacinto DRAx SoC that consolidates these functions from several ECUs, would be a befitting example here.
- Application Processors: The modern digital cockpit system has intense processing power to accomplish various functions. For example, managing multiple audio and video input/output, managing the ADAS and driver monitoring features, powering speech and image recognition capabilities, supporting real-time navigation & more.
- The Communication Interfaces: The modern-day vehicle is a complex network of interconnected subsystems that constantly communicate with each other to function efficiently.
The role of communication interfaces in enabling seamless transmission of data, within and outside a vehicle, cannot be emphasized enough. From controlling the infotainment display to exchanging vehicle data securely over the cloud, to adjusting HVAC system – we need specific Communication interfaces to manage various functions within a car.
Let us take a quick look at some important communication interfaces required in an automotive cockpit system:
Communication Mode Functions Managed Features CAN Vehicle Connectivity and Vehicle Diagnostics ·Used by controllers, processors, sensors, engine control unit, etc. to communicate via specific messages ·Operates at speeds ≥1 Mbps
Automotive Ethernet/ DoIP Vehicle Connectivity, In-vehicle infotainment systems · Ethernet is ideally used for mid bandwidth transmission of high-speed data · Used in applications such as navigation systems and control, rear camera, infotainment, etc.
· Speed: 100 Mb/s
Audio and Video Bridge (AVB) For live audio and video streaming · Ideal for streaming timely and continuous audio/video (A/V) content especially for bandwidth intensive applications without lags or buffering Bluetooth
BLE
NFC
USBSupporting User Experience functions · Seamlessly connect portable devices such as smartphones with the car in an energy-efficient manner · Replaces the need for physical cables
· Bidirectional communications between car and the devices
Wi-Fi
CellularManaging data communications with the cloud server for FOTA updates, telematics, etc. ·For embedded connectivity and faster transmission of data · Have been used for sending alerts like automatic crash and door unlocking notification
- The Software Module:
- Operating System: This is usually a set of RTOS and Non-RTOS, that can manage different functionalities, completely in isolation of each other, while sharing the hardware resources. This process is facilitated by means of virtualization, which has been explained in the subsequent section.
For example, all the time critical functionalities related to Instrument Cluster, Collision warning, HVAC, Telematics, etc. can be managed by an RTOS like QNX, Integrity. Meanwhile, functions which are less time-critical such as infotainment and Driver Monitoring system can be managed by a Non-RTOS such as Linux, Windows. This type of OS isolation offers great benefits in terms of simpler system design and cost savings due to resource sharing.
- Middleware: This layer offers support for features like multimedia, voice assistance, integration with smartphone (Apple CarPlay, Android Auto,) Bluetooth, UI framework, web browser, etc.
- Virtualization: Virtualization is the key mechanism that enables a digital cockpit to manage a plethora of functions using shared hardware resources and peripherals. Under this, multiple Operating systems, including RTOS & Non-RTOS can be run on a common hardware platform. This not only makes it easy to develop and manage the components but also helps in optimizing the cost and enhancing the performance of the cockpit systems.
Typically, the modern-day providers of digital cockpit solutions follow one of the two approaches for virtualization:
- The Hypervisor Approach: A hypervisor is a thin layer between the operating systems and the hardware. A hypervisor software helps multiple OS environments managing the cluster, infotainment, HUDs and other digital systems to function as isolated systems. Such an isolation is very useful – In case one of the applications crashes, the remaining applications can still function normally without getting affected.
- Virtualization using Multiple Core Application Processors: Instead of a dedicated platform like hypervisor, this approach makes use of multiple core application processors for OS isolation and partitioning of resources. Multicore operating systems allow for virtualization by mapping different applications to the different core in the multicore.
Virtualization using Hypervisor
- Operating System: This is usually a set of RTOS and Non-RTOS, that can manage different functionalities, completely in isolation of each other, while sharing the hardware resources. This process is facilitated by means of virtualization, which has been explained in the subsequent section.
Challenges in Designing a Digital Cockpit
At present, the stakeholders in the automotive industry are faced with a host of technical and business challenges associated with designing a robust and secure digital cockpit solution. Let us take a quick glance at some critical challenges:
- Hardware & Software design, as per the ISO 26262 FuSa guidelines:
Adhering to the Functional Safety (FuSa) guidelines, as per the ISO 26262 Standard, is very critical for any automotive application development project.
Any hardware or software component that is part of an automotive application should have an ASIL defined for itself based on its safety-criticality.
Also Read our blog: Understanding How ISO 26262 ASIL is Determined for Automotive Applications
In modern automotive applications like Digital cockpit, a single ECU handles multiple functions. In such a scenario, there are possibilities of software and hardware components with different safety criticality (ASIL ratings) to coexist. These components of varying ASIL ratings may interfere with each other, leading to safety violations.
This is particularly challenging when the components with differing ASIL ratings are sharing a common CPU and memory resources.
If these potential challenges are not properly addressed at the design stage, these may lead to safety hazards later on.
- Cost Optimization (Licensing cost, Per Unit Cost, Development cost):
Development of digital cockpit solution using the Hypervisor approach for OS virtualization is still a costly proposition.
The cost factors associated with Hypervisor involves – virtualization licenses, cost required for implementation of advanced features such as V2X, and costs based on the number of cores and type of OS.
An alternate approach to optimize cost could be to use a free RTOS. But one needs to ensure its reliability in terms of performance, speed of execution, and robustness.
Custom Development of Digital Cockpit Solutions Can Give You an Upper Edge in the Market
The Build vs Buy dilemma is pertinent in the domain of automotive components as well. Our automotive experts are of the opinion that custom-designing a digital cockpit for cars can be a game-changer for OEMs. Listed below are some advantages offered by this approach:
- Degree of freedom – When you embark on the custom development of a digital cockpit, you receive exclusive IP rights for the product. This facilitates the scalability of the solution based on your future needs. On the other hand, an off-the-shelf solution may not provide you complete IP rights to the system.
- Cost of Ownership – The Total Cost of Ownership (TCO) of a digital cockpit solution is directly proportional to the cost per unit, number of units ordered and support/maintenance costs. Investment in an off-the-shelf car cockpit system may not guarantee you lower TCO.
For instance, if your business desires the inclusion of certain features that are not available in the ready-to-deploy version offered by a vendor, you may have to custom-develop those modules.
Another point to note is related to upgrades to off-the-shelf systems. When upgraded versions of your car cockpit solution are released in the market, you will have to identify possibilities of getting your system up to date as well. This involves further development and testing costs.
Considering the scenarios listed above, it is clear that investing in a custom-designed digital cockpit may incur higher costs upfront. However, in the long run, the solution can be effortlessly maintained by your organization as you own the product. This offers unparalleled long-term stability and control.
It is important to partner with reliable automotive engineering service providers like Embitel for custom-development of digital cockpit solutions. Our experience in the design and development of automotive applications for connected cars and EVs exceed 14 years.
If you have a business challenge related to digital cockpit, telematics, FOTA update, HVAC, infotainment system, driver assistance, etc. please reach out to sales@embitel.com for a free consultation.