ASPICE (Automotive SPICE) is a process assessment and improvement framework designed specifically for the automotive industry. It ensures that software and system development processes meet high-quality, reliability, and safety standards.
From being a fancy addition to cars, software now determines the value of the car. Whether the car has a 360-degree camera or advanced ADAS features makes or breaks a deal.
Such rapid innovation in automotive software has been possible partly because of the standardization brought about by ASPICE. And the safety threats that such software poses is mitigated by following the ISO 26262 standard.
As a matter of fact, both standards are indispensable for the automotive industry. And most of the time, both the standards must be followed simultaneously.
ASPICE provides an ideal framework to implement the ISO 26262 standard as it covers the entire system development. The functional safety lifecycle can be matched with the V-model followed by Automotive SPICE.
We've discussed two distinct yet interconnected concepts—one focused on overall software quality and the other on safety. But how do they relate? ASPICE vs. ISO 26262—do they complement each other, or do they serve entirely different purposes? Can they coexist within the same development framework?
ASPICE in the Era of Software Driven Vehicle
We have all heard of ‘software-driven vehicle’ aka SDVs. In fact, most modern vehicles on the road are more or less SDVs.
Let’s take an example of an electronic parking brake. This module replaces a manual handbrake with an electronically operated parking brake. While doing so, the engineers develop an ECU with scores of algorithms such as auto-apply, Gradient-based apply, Auto-hold and more.
Let’s take the example of an Electronic Parking Brake (EPB)— a system that replaces the traditional manual handbrake with an electronically controlled mechanism. Instead of relying on mechanical force, the EPB is governed by an ECU running complex software algorithms. These include:
- Auto-apply – Automatically engaging the parking brake when the vehicle stops.
- Gradient-based apply – Adjusting brake force depending on road incline.
- Auto-hold – Preventing the vehicle from rolling on slopes without continuous brake pedal pressure.
- Dynamic braking integration – Coordinating with other braking systems (e.g., ABS, ESC) for emergency braking situations.
While these features enhance safety and convenience, they introduce significant software development challenges.
Why ASPICE is Essential for SDVs
As automotive software grows in complexity, so do the risks of bugs, inconsistencies, and cybersecurity vulnerabilities. ASPICE framework is designed to mitigate such risks in the course of development.
ASPICE provides a structured framework for software development, ensuring that automotive ECUs like Electronic Parking Brake are designed with:
- Robust software architecture for long-term reliability
- Traceability from requirements to implementation and testing
- Process consistency across different suppliers and development teams
- Rigorous validation to prevent failures in safety-critical systems
ASPICE and the V-Model Development Approach
To manage the complexity of SDV software, ASPICE follows a V-model development cycle:
- System Requirements Analysis (SYS.1): Defining high-level functional and non-functional requirements.
- Software Requirements Analysis (SWE.1): Converting system-level needs into software-specific requirements.
- Software Architecture and Detailed Design (SWE.2 & SWE.3): Structuring software components and defining their interactions.
- Software Integration and Testing (SWE.4 & SWE.5): Ensuring all components work together seamlessly.
- System Validation (SYS.5): Verifying that the software meets safety, security, and performance standards.
For critical automotive functions like EPB, ADAS, or Battery Management Systems (BMS), an ASPICE Level 2 or Level 3 certification is often required by OEMs and Tier-1 suppliers.
Role of ASPICE and ISO 26262 in Improving Quality and Safety of Automotive Applications
The role of ASPICE and ISO 26262 standards in the automotive industry is synergistic. By following ISO 26262 standard it is ensured that automotive E/E systems are safe and capable of performing to the required safety levels. While ASPICE enhances the overall process capability and quality of software development.
Together, they form a robust framework for developing high quality safety-critical automotive ECUs. This integrated approach is essential for automotive manufacturers and suppliers striving to meet the growing demands for safety and quality in an industry.
Understanding the role and interaction of these standards is crucial for automotive manufacturers and suppliers.
ISO 26262: The Automotive Functional Safety Standard
ISO 26262 is an international standard for functional safety in electrical and electronic (E/E) systems within road vehicles. Originating from the generic functional safety standard IEC 61508, ISO 26262 is tailored specifically for the automotive context.
Safety Lifecycle Management: It covers the entire lifecycle of automotive E/E systems, from conceptual design to production and operation. It emphasizes identifying and mitigating risks associated with potential malfunctions of E/E systems that could lead to hazardous situations.
Hazard Analysis and Risk Assessment: ISO 26262 involves systematic hazard analysis and risk assessment to determine Automotive Safety Integrity Levels (ASILs), which dictate the stringency of safety measures to be applied.
Safety-Oriented Design: The standard prescribes safety-oriented design principles and methods, including requirements specification, design, implementation, verification, validation, and configuration management.
ASPICE: Enhancing Software Process Capability
ASPICE is a framework for assessing and improving software development processes in the automotive industry. It is based on the ISO/IEC 15504 standard (SPICE) and tailored for automotive software development.
Process Capability Levels: ASPICE provides a process capability framework that assesses processes on a scale from Level 0 (Incomplete) to Level 5 (Optimizing). Achieving higher capability levels indicates more mature, consistent, and effective software development processes.
Quality Improvement: By following ASPICE, organizations can systematically improve their software development processes, leading to higher quality software products. It focuses on areas like requirements management, design, implementation, testing, and maintenance.
Supplier Assessment: ASPICE is often used by automotive manufacturers to assess and select suppliers, ensuring that the suppliers’ software development capabilities meet certain standards.
ASPICE vs ISO 26262: Integration and Synergy
The integration of ISO 26262 and ASPICE is crucial in the automotive industry for several reasons:
- Complementary Objectives: While ISO 26262 focuses on functional safety, ASPICE aims at process quality and capability. Together, they ensure that automotive software is not only safe but also developed using high-quality processes.
- Mutual Reinforcement: Compliance with ISO 26262 can be facilitated by ASPICE’s process improvement framework. A higher process capability level in ASPICE can lead to more effective implementation of safety requirements as outlined in ISO 26262.
- Unified Approach to Safety and Quality: Integrating ISO 26262 and ASPICE allows organizations to adopt a holistic approach, where safety considerations are embedded into every stage of the software development lifecycle, enhanced by ASPICE’s focus on process quality.
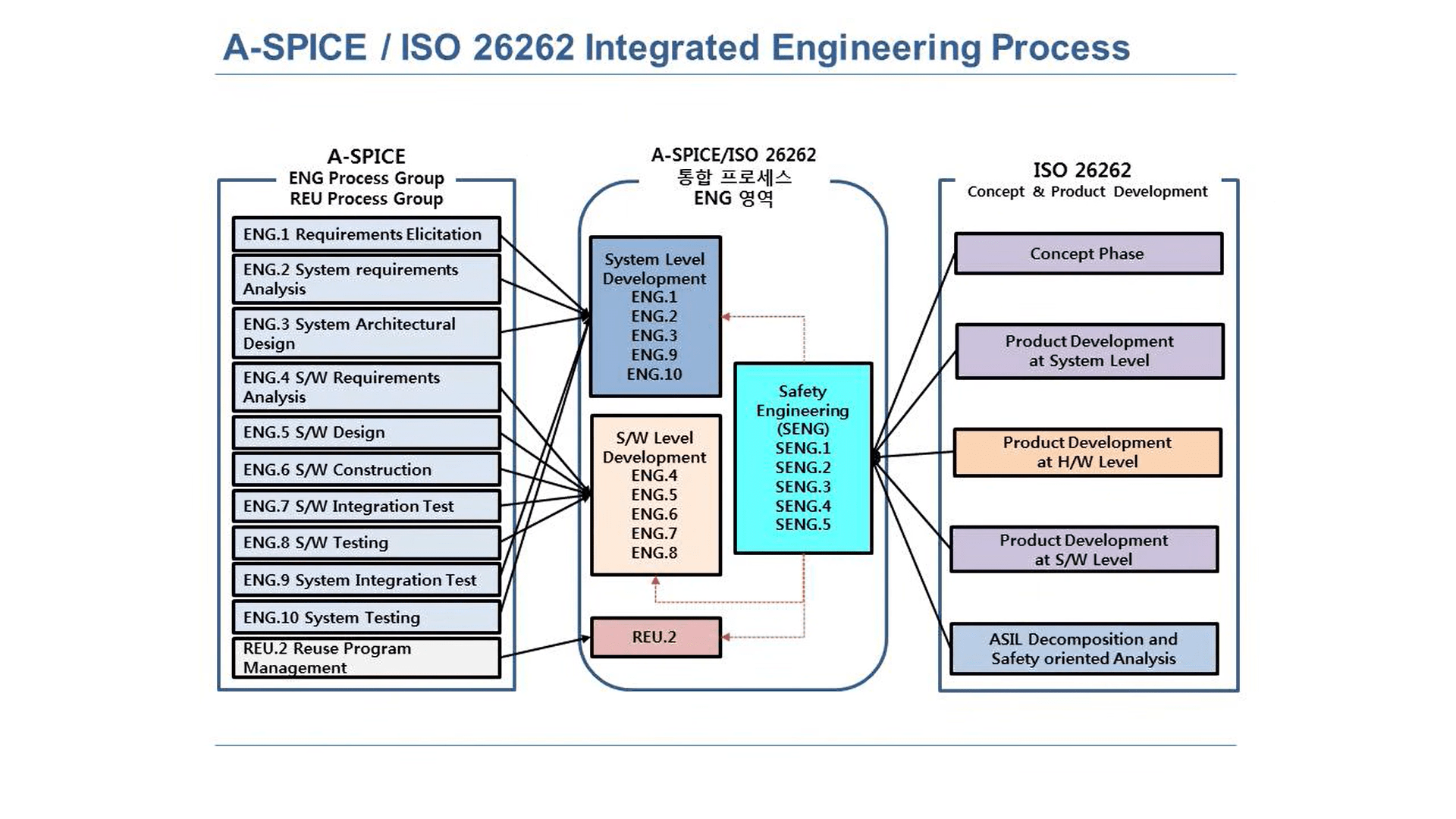
As is clear from the image above, the ISO 26262 lifecycle can be matched with the V-model followed by Automotive SPICE.
The additional items that ISO 26262 brings to the table are mostly related to the concept phase. They include:
- Item Definition: It is a list of the system, sub-systems, functional dependencies, and various such attributes. The information contained in the item definition document, serves as an input for the HARA process.
- Failure Mode Effect Analysis (FMEA): FMEA is an inductive analysis method to find the causes and effects of a failure. It also contributes to the identification of functional and non-functional requirements, which might not have been identified during HARA.
- Failure Modes, effects, and diagnostic analysis (FMEDA): Failure Modes, Effects, and Diagnostic analysis (FMEDA), is an ideal method for the derivation of Hardware Architecture Metrics like PMHF (Probabilistic Metrics for Hardware Failures), SPFM (Single-Point Fault Metric) and LFM (Latent Fault Metric).
- Failure Tree Analysis (FTA): Fault Tree Analysis (FTA) is an example of deductive failure analysis where root case of the fault is depicted using Boolean logic.
- Hazard Analysis and Risk Analysis (HARA): The purpose of HARA is to identify the malfunctions that could possibly lead to E/E system hazards and assess the risk associated with them.
Together with ISO 26262 and ASPICE, there are approximately 250 work products and 60 process to take care of which is indeed a sheer quantity of work.
The ISO 26262 mandated safety lifecycle is followed simultaneously with ASPICE. At every stage of V-cycle, certain analyses recommended by ISO 26262 standard are performed alongside ASPICE processes. For instance, a hazard analysis is performed as an extension to risk management (ASPICE). More analyses like FMEA and FMEDA are introduced to derive safety goals, failure in time (FIT) and certain hardware metrics such as SPFM, LFM and PMHF.
Moreover, the System Requirement specification would also include safety requirements. The Verification and Validation processes would also follow the methodologies as mentioned in the ISO 26262 standard. The diagram makes the overlapping of ISO 26262 and ASPICE clearer:
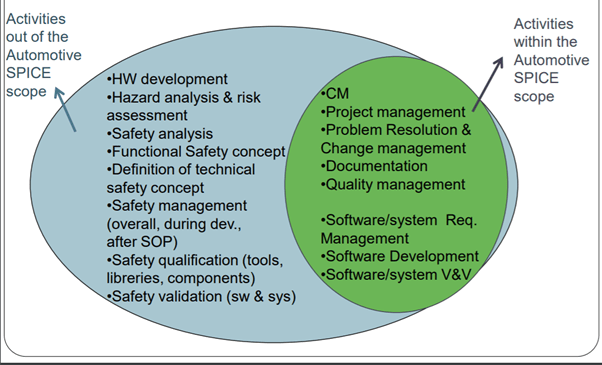
ASPICE vs ISO 26262: What are the differences?
ISO 26262 addresses safety, while ASPICE focuses on ensuring the development process is mature and efficient. Together, they ensure that automotive systems like Brake ECUs are both safe and well-built.
To implement both standards effectively, it is important to understand their contrast. ASPICE vs ISO 26262—how do they differ in focus, scope, and implementation? Recognizing this difference ensures that both functional safety and efficient development practices are adequately addressed in automotive systems.
Focus
ISO 26262 standard is all about functional safety. It ensures that automotive systems like Brake ECUs perform reliably under all conditions, even when a component fails. For example, if a sensor fails in the Brake ECU, ISO 26262 ensures the system still operates safely by having backup systems or fail-safe measures in place.
ASPICE, on the other hand, focuses on the maturity of development processes. It’s about making sure the software development is structured, efficient, and produces reliable results. Take, for instance, the infotainment system in a car. While it’s not as safety critical as a Brake ECU, ASPICE ensures the software behind it is developed following a mature and consistent process, which helps avoid bugs and performance issues.
Scope
The scope of ISO 26262 is strictly related to safety-critical systems. It’s designed to ensure that any system whose failure could directly endanger human life, like airbags, steering control, or Brake ECUs, is developed with the most stringent safety standards.
For example, when developing an autonomous driving system, ISO 26262 ensures that if something goes wrong with the sensors or processing units, there are safety mechanisms in place.
In contrast, ASPICE vs ISO 26262 differs in that ASPICE applies to all automotive software projects, not just safety-critical ones. It helps in refining the development processes of automotive software. For example, ASPICE ensures that the software behind a car’s entertainment system is tested thoroughly and developed using efficient processes.
Implementation
The implementation of ISO 26262 is centered around a safety lifecycle. This includes activities like Hazard Analysis and Risk Assessment (HARA), and the inclusion of safety mechanisms based on multiple analyses.
Safety mechanisms usually include redundancy or fault-tolerant designs that are integrated to mitigate identified risks as per the assigned ASIL. The standard clearly categorizes safety-criticality from ASIL A to ASIL D, the latter being the most safety-critical.
ASPICE takes a slightly different approach. It focuses on maturity levels for development processes. It evaluates key processes like requirements management, design, testing, and validation to ensure they are structured and efficient. The model promotes continuous improvement through maturity stages, from Level 1 (Initial) to Level 5 (Optimizing).
For instance, in the case of a powertrain control system, ASPICE implementation would ensure that the development process for the system is thoroughly documented. This, in turn, implies that all steps are taken to ensure the final product performs well.
Risk Management
ISO 26262 standard centers its risk management efforts on safety risks. It involves assessing potential hazards and assigning Automotive Safety Integrity Levels (ASILs) to each risk.
For instance, a risk like a brake system failure might be assigned a high ASIL (e.g., ASIL D), meaning the system must be designed with extremely high levels of redundancy and fault tolerance as per the ISO 26262 standard. This ensures that the risks are adequately mitigated, and the system operates safely.
While ASPICE doesn’t directly focus on safety risks, it assesses process-related risks. For example, if the testing process is not thorough enough, it could result in undetected defects. ASPICE addresses these risks by ensuring the processes are documented, controlled, and improved over time. This makes the development process more predictable and reduces the risk of defects.
Verification and Validation
In a safety-critical development program, verification and validation (V&V) are deeply tied to safety goals. It checks if the safety requirements for the system are met. The standard clearly mandates testing methods like fault-injection testing, basis the ASIL value assigned to the solution. For an ASIL D system, MC/DC (Modified Condition/Decision Coverage) test is mandatory while it is only recommended for lower ASILs.
In terms of V&V, ASPICE implementors focuses on verifying the processes themselves. It ensures that the development process is properly defined, followed, and tested. Generally speaking, ASPICE implementation would verify that system development goes through each phase, from initial requirements to final testing, without skipping steps. If any process is weak, the ASPICE standard ensures that it is improved.
What Does ASPICE 3.1 Change in Terms of Integration with ISO 26262?
The newer version of ASPICE adds enhanced support for ISO 26262 implementation. By implementing ASPICE, a major part of ISO 26262 implementation can also be fulfilled.
Requirement Elicitation as per ASPICE corresponds to Item definition in ISO 26262 standard. In the latest version of ASPICE, requirement elicitation offers strong support in performing item definition. It implies that a large part of these two activities can be merged which would result in reduced effort and time.
Similarly, there are certain ASPICE processes that offer medium level support to their corresponding activity in ISO 26262 implementation. One example is software unit verification, where few of the guidelines overlap while others don’t. Most of the ASPICE processes are in the medium support category such as system architectural design, integration test etc.
However, there are couple of ISO 26262 activities that are still quite distant from ASPICE process. They include functional safety concept and technical safety requirement specifications.
Looking at the overall picture, it is quite clear that the automotive industry as a whole is pushing the integration of ASPICE and ISO 26262. Still, there are certain inherent challenges when it comes to integration of ASPICE and ISO 26262. Let’s look at them.
Challenges in ASPICE and ISO 26262 Integration and How to Overcome Them
Integrating ISO 26262 and ASPICE can be challenging due to several factors, including differences in scope, terminology, and evaluation criteria.
ISO 26262 is a standard that mandates various testing methodologies, software architectural design and implementation guidelines etc. to ensure functional safety concerns are met at the system level.
Whereas ASPICE is more focused on improving the quality of the automotive software not only at the system level but also at the project and org level.
These fundamental differences thus lead to challenges in scenarios where ASPICE and ISO 26262 standard are required to be implemented. Let’s explore these challenges.
Scope and FocusISO 26262 primarily focuses on functional safety aspects, addressing hazards and risks associated with electrical and electronic systems in vehicles. On the other hand, ASPICE focuses on improving software development processes. Integrating these two standards requires aligning their different scopes and ensuring a comprehensive approach.
Challenge: The automotive manufacturer needs to determine how to combine safety-related activities from ISO 26262 (e.g., hazard analysis, safety requirements management) with the software development activities defined in ASPICE (e.g., requirements engineering, testing). They must establish a clear mapping and coordination between safety-critical aspects and software development processes.
Terminology and ConceptsISO 26262 and ASPICE use different terminology and concepts, leading to potential confusion and misalignment among project stakeholders. Harmonizing these differences is crucial for effective integration.
Challenge: The automotive manufacturer faces the challenge of establishing a common language and understanding among team members. For instance, aligning the terminology of safety goals, safety requirements, and functional safety concepts from ISO 26262 with the software development terminology of requirements, design, and testing from ASPICE.
Evaluation Criteria and AssessmentsISO 26262 and ASPICE have different evaluation criteria and assessment methods. ISO 26262 includes safety integrity levels (ASILs) and the concept of safety case, while ASPICE uses process capability levels and process assessments. Integrating these evaluation approaches requires careful consideration.
Challenge: The automotive manufacturer needs to determine how to harmonize the assessment methods and criteria to ensure a unified evaluation of both functional safety and process capability. They must establish a consistent evaluation framework that satisfies the requirements of both ISO 26262 and ASPICE.
Training of cross-functional teams and knowledge integrationISO 26262 and ASPICE are highly technical standards with complex concepts and requirements. Training team members from different disciplines, such as software development, system engineering, functional safety, and quality management, may require varying levels of technical understanding.
Challenge: Integrating the knowledge gained from ISO 26262 and ASPICE training programs can be challenging. Team members may struggle to understand how the requirements and processes of these standards align and complement each other. Facilitating discussions, workshops, or practical exercises that allow team members to apply their knowledge in an integrated manner can help overcome this challenge.
These challenges must be taken up by the functional safety manager and ASPICE consultant working on the project. They can work together to mitigate the challenges involved in integrating ASPICE and ISO 26262. Here’s a few pointers on how they can approach these challenges:
Gap analysis and alignment: The ASPICE consultant can conduct a thorough gap analysis to identify the areas of misalignment or differences between ASPICE and ISO 26262. They can collaborate with the functional safety manager to create an integration plan that maps the processes and activities of ASPICE to the corresponding functional safety activities in ISO 26262.
Training and knowledge sharing: The functional safety manager, being well-versed in ISO 26262, can provide specialized training to the team members involved in the integration effort. The ASPICE consultant can complement this by providing training on ASPICE and its process improvement methodologies.
Documentation and evidence management: Both the functional safety manager and the ASPICE consultant must collaborate to establish a unified documentation framework. They can define the necessary templates, artifacts, and traceability requirements that align with the expectations of both ASPICE and ISO 26262.
Process harmonization: The commonalities and overlaps between the two standards should be identified and streamlining of activities can be performed to avoid duplication and optimize resource utilization.
The Road Ahead
ASPICE covers the broad aspects of software development and ISO 26262 can expand its safety aspect. These two standards are different in many regards such as cost and time implications, assessments etc. However, they have quite a few similarities that include process areas such as configuration and change management and commitment towards achieving bi-directional traceability between the work-products.
Several tools and templates are also available that make the integration of ASPICE and ISO 26262 easier for the development and compliance teams. Functional Safety consultancy organizations leverage these tools and templates to help the OEMs and suppliers in achieving the required compliance.
By integrating ASPICE and ISO 26262, automotive projects can benefit from enhanced process maturity, improved software quality, effective risk management, and compliance with safety standards. These integrations enable organizations to develop safer and more reliable automotive systems by aligning their software development processes with functional safety requirements.